How a Fuel Sensor for Trucks 2025 Can Reduce Fuel Wastage & Improve Efficiency
Are you looking to enhance the efficiency and maximize the performance of your truck fleet? If so, choosing the perfect fuel sensor is of utmost importance. A fuel sensor is a device that measures and monitors the level of fuel in your trucks, enabling you to make informed decisions and optimize fuel usage. But with so many options available in the market, how do you choose the right fuel sensor for your trucks?
In this ultimate guide, we will walk you through everything you need to know to make the right choice. We’ll discuss the different types of fuel sensors, their features, and their benefits. You’ll learn about the factors to consider when selecting a fuel sensor, such as accuracy, durability, and compatibility with your trucks’ systems. We’ll also guide you on installation and maintenance, ensuring that you get the most out of your fuel sensor in the long run.
By the end of this guide, you’ll have all the knowledge and tools necessary to choose the perfect fuel sensor for your trucks, increasing fuel efficiency, reducing costs, and ultimately maximizing performance.
Importance of Choosing the Right Fuel Sensor
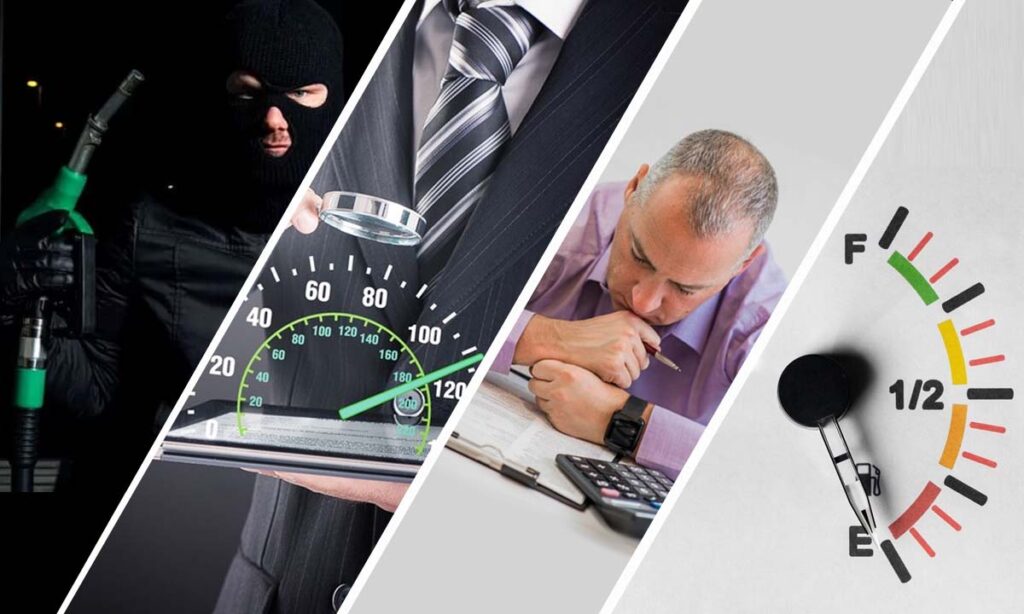
Selecting the right fuel sensor for your truck fleet is crucial for a multitude of reasons. First and foremost, an efficient fuel management system hinges on accurate readings of fuel levels. Inaccurate measurements can lead to over-fueling or under-fueling, both of which can significantly impact operational costs and vehicle performance. By choosing a reliable fuel sensor, fleet managers can ensure that they have real-time data at their fingertips, allowing for better decision-making regarding fuel procurement, route planning, and overall fleet management. This accuracy not only saves money but also optimizes fuel usage, leading to reduced environmental impact.
Another important aspect is the sensor’s role in preventing fuel theft and loss. In many fleets, fuel is one of the largest operational expenses, and any loss can directly affect profitability. A good quality fuel sensor provides alerts and data that can help in identifying irregularities in fuel consumption, potentially indicating theft or leaks. This monitoring capability helps businesses to mitigate losses and improve accountability among personnel, thereby enhancing the security of fuel assets.
Moreover, the right fuel sensor contributes to the longevity and performance of the truck. Sensors that accurately monitor fuel levels can prevent the engine from running dry, which can cause significant damage and costly repairs. With a good sensor, you can maintain optimal fuel levels, ensuring that trucks operate efficiently. This not only enhances the lifespan of the vehicle but also maximizes its performance on the road, leading to better service delivery and customer satisfaction.
Different Types of Fuel Sensors Available
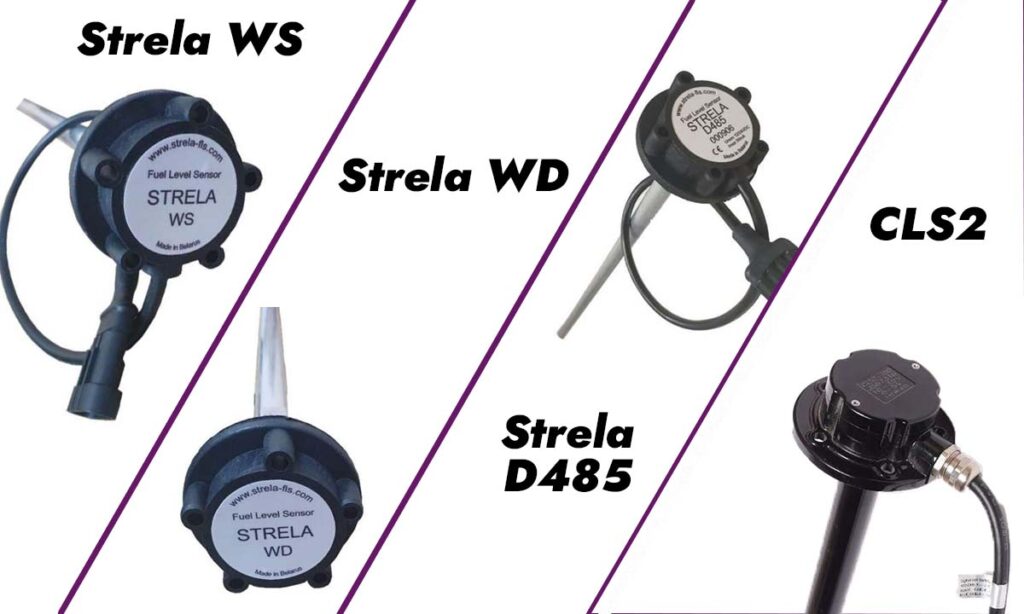
When it comes to fuel sensors, there are several types available, each with unique features and applications. The most common types include capacitive, resistive, ultrasonic, and mechanical sensors. Capacitive fuel sensors work by measuring the capacitance change as the fuel level rises or falls. These sensors are highly accurate and can be used in various fuel types, making them suitable for diverse truck fleets. Their non-contact design also adds to their longevity, as they are less prone to wear and tear.
Resistive fuel sensors, on the other hand, function based on the principle of resistance change due to varying fuel levels. These sensors are generally more affordable and easy to install but can be less accurate than capacitive types. They are a popular choice for smaller fleets or older truck models. Ultrasonic sensors employ sound waves to determine fuel levels. They are known for their high accuracy and are especially useful in environments where traditional sensors may struggle, such as in tanks with irregular shapes.
Lastly, mechanical fuel sensors, such as float-based systems, have been used for many years. While they are reliable and simple in design, mechanical sensors can be prone to failure and inaccuracies over time, especially in harsh conditions. Understanding these different types of fuel sensors can help fleet managers choose the right solution based on their specific needs, budget, and operational requirements.
Factors to Consider When Choosing a Fuel Sensor
Choosing the right fuel sensor involves careful consideration of several critical factors. One of the most important aspects to evaluate is accuracy. The precision of a fuel sensor can dramatically affect operational efficiency. A sensor that provides consistent, reliable readings allows for better fuel management and cost savings. Fleet managers should look for sensors that have been validated through tests and reviews to ensure they meet industry standards for accuracy.
Durability is another vital factor to consider. Trucks often operate in tough environments, which means that the fuel sensor needs to withstand vibrations, temperature fluctuations, and exposure to various fuels. Sensors made from high-quality materials that are resistant to corrosion and wear will generally provide a longer lifespan and require less frequent replacements, which can significantly reduce total ownership costs.
Compatibility with existing systems is also essential. Fleet managers should ensure that the sensor they choose can easily integrate with the truck’s onboard diagnostics and fuel management systems. This compatibility not only simplifies installation but also enhances the functionality of the sensor, allowing for features such as real-time monitoring and alerts. Conducting thorough research and possibly consulting with manufacturers can help in selecting a fuel sensor that aligns with the fleet’s technological framework.
Understanding Fuel Sensor Specifications and Features
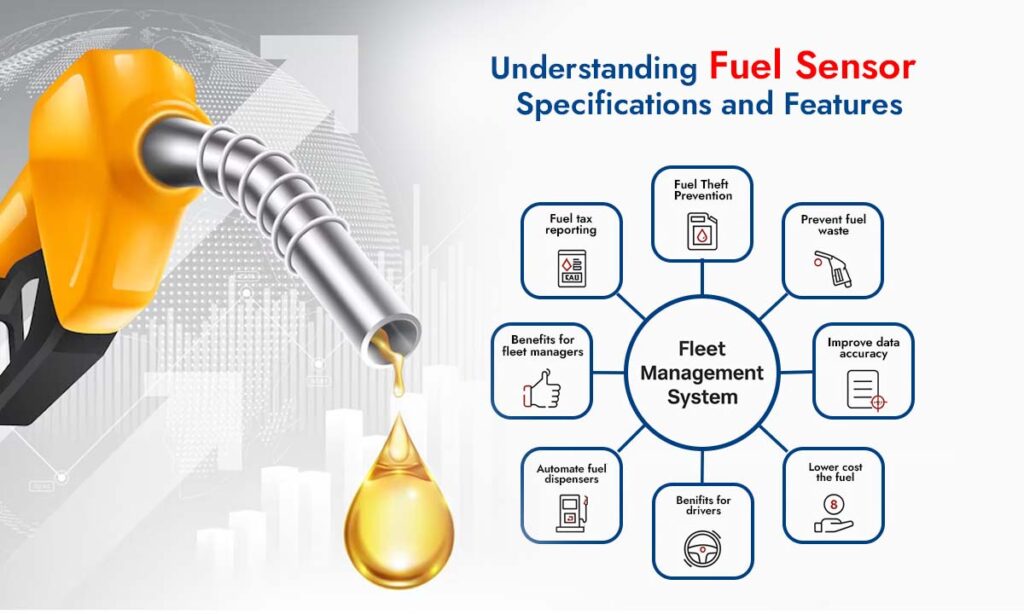
When diving into the specifications of fuel sensors, it’s important to familiarize yourself with terms like measurement range, output signal type, and power requirements. The measurement range indicates the minimum and maximum fuel levels that the sensor can accurately detect. It’s crucial to select a sensor with a range that accommodates the tanks used in your fleet. A sensor that is too limited may fail to provide accurate readings during low fuel conditions, while one with an excessively high range may not fit well in smaller applications.
The output signal type is another significant specification. Different sensors may offer various output types such as analog, digital, or pulse-width modulation. Understanding the output signal is essential for ensuring compatibility with your existing fleet management software and for making sure the data can be easily interpreted and utilized. This feature can greatly enhance the overall effectiveness of fuel monitoring practices within your fleet.
Power requirements should also be taken into account. Some fuel sensors operate on low voltage while others may require more robust electrical setups. Selecting a sensor that matches the power capabilities of your trucks is essential to avoid potential installation issues and to ensure reliable operation. Additionally, features such as built-in alarms, data logging capabilities, and wireless connectivity can further enhance functionality, providing fleet managers with the tools needed to optimize fuel usage effectively.
How does a fuel sensor work in trucks?
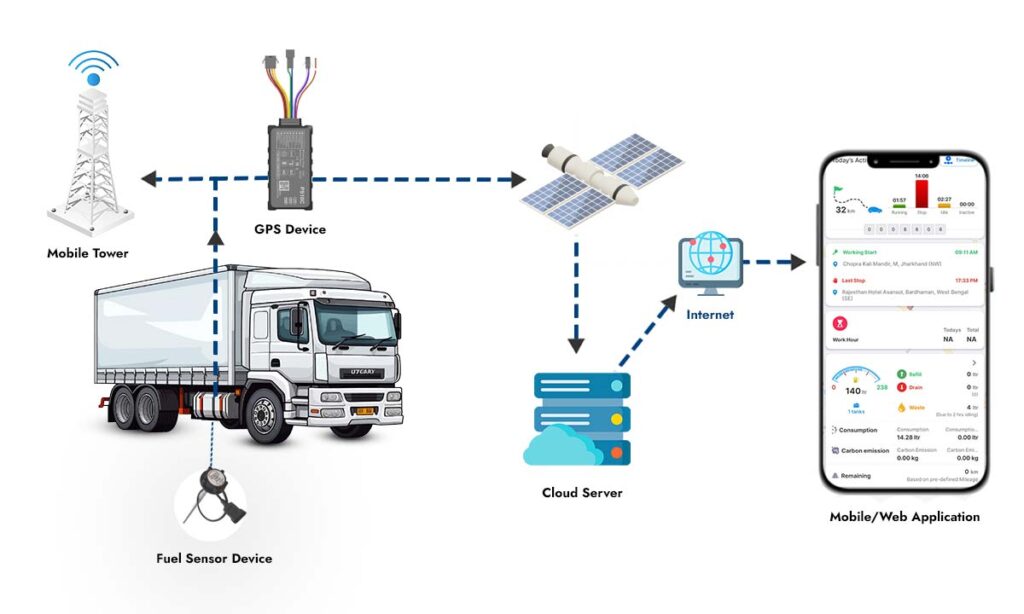
Here’s a simple overview of how a fuel sensor works in a truck, based on the flow shown in the diagram:
- Sensor in the Tank
- A fuel sensor is installed inside the truck’s fuel tank. Common types include capacitive or ultrasonic sensors. They measure the fuel level by detecting changes in electrical signals or sound waves, depending on the technology used.
- Data Capture
- As the fuel level changes (due to consumption, refilling, or leakage), the sensor continuously records these level variations.
- Connection to GPS/Telematics Device
- The sensor is wired (or wirelessly connected) to a GPS/telematics device. This device aggregates data from various sensors—fuel level, location, speed, and engine diagnostics.
- Data Transmission via Network
- The GPS/telematics device sends the collected sensor data through:
- Cellular networks (using a mobile tower), or
- Satellite communication (in areas with low cellular coverage).
- The GPS/telematics device sends the collected sensor data through:
- Cloud Server Processing
- The data travels securely over the internet to a cloud server, where it is stored and processed.
- The server can perform advanced analytics—detecting fuel theft, calculating consumption rates, and generating alerts.
- Viewing on Mobile/Web App
- Fleet managers, owners, or drivers log in to a mobile or web application connected to the server.
- They see real-time metrics: current fuel level, refills, drains, consumption trends, and overall vehicle location and status.
- Informed Fleet Management
- Armed with accurate, real-time information, managers can:
- Prevent fuel theft by getting instant alerts for sudden drops.
- Plan fueling stops more efficiently.
- Optimize routes and driving behavior to reduce overall fuel costs.
- Armed with accurate, real-time information, managers can:
In short, the fuel sensor tracks the tank’s fuel level, the GPS/telematics device sends that data to the cloud, and the application displays it in easy-to-read dashboards—making it simpler to reduce fuel wastage, detect anomalies, and manage fleets effectively.
Maintenance and Troubleshooting Tips for Fuel Sensors
Maintaining your fuel sensors is essential for ensuring long-term performance and reliability. Regular inspections should be part of your routine maintenance schedule. Check for any signs of wear, corrosion, or damage to the sensors and their connections. This is particularly important for sensors exposed to harsh environmental conditions, as they may be more susceptible to failure. Keeping the sensor clean and free from obstructions can also help maintain accurate readings.
If you notice any discrepancies in fuel level readings, troubleshooting should be your first step. Start by checking the electrical connections to ensure there are no loose wires or corroded terminals. Verify that the sensor is correctly calibrated according to the manufacturer’s specifications. In some cases, a simple recalibration can resolve issues related to inaccurate readings. If problems persist, consulting the troubleshooting section of the installation manual can provide valuable insights into common issues and their solutions.
In addition to these checks, it’s crucial to keep software updated if your sensors are integrated with a digital monitoring system. Manufacturers often release updates that improve sensor performance or resolve known issues. Regular software updates can enhance the functionality of your fuel sensors, ensuring they operate efficiently and accurately over time. By adhering to these maintenance and troubleshooting tips, you can extend the life of your fuel sensors and maximize their effectiveness in your fleet management strategy.
Benefits of Using a High-Quality Fuel Sensor
nvesting in a high-quality fuel sensor presents numerous benefits that can significantly enhance the efficiency and performance of your truck fleet. One of the primary advantages is improved accuracy. High-quality sensors provide precise measurements of fuel levels, enabling more effective fuel management practices. This accuracy reduces the chances of over-fueling or running out of fuel, both of which can lead to unnecessary costs and operational disruptions.
Another benefit is enhanced durability and reliability. High-quality sensors are built to withstand the rigors of transportation environments, minimizing the need for frequent replacements. This resilience translates to lower maintenance costs and a more reliable data stream, which is crucial for effective fleet management. Additionally, many premium sensors come equipped with advanced features such as remote monitoring and alerts, further enhancing their utility in operational management.
Finally, the adoption of high-quality fuel sensors can lead to substantial long-term savings. By optimizing fuel consumption and reducing waste, fleets can lower their overall operating costs. These savings can have a significant impact on profitability, particularly for large fleets where even small efficiencies can translate into substantial financial gains. Overall, high-quality fuel sensors are an investment that pays dividends in efficiency, reliability, and cost savings.
Top Fuel Sensors from Pictor Telematics
At Pictor Telematics, we provide high-precision fuel sensors designed for fleet management. Here are our best solutions:
1. Fuel Level Sensor: Strela Ws
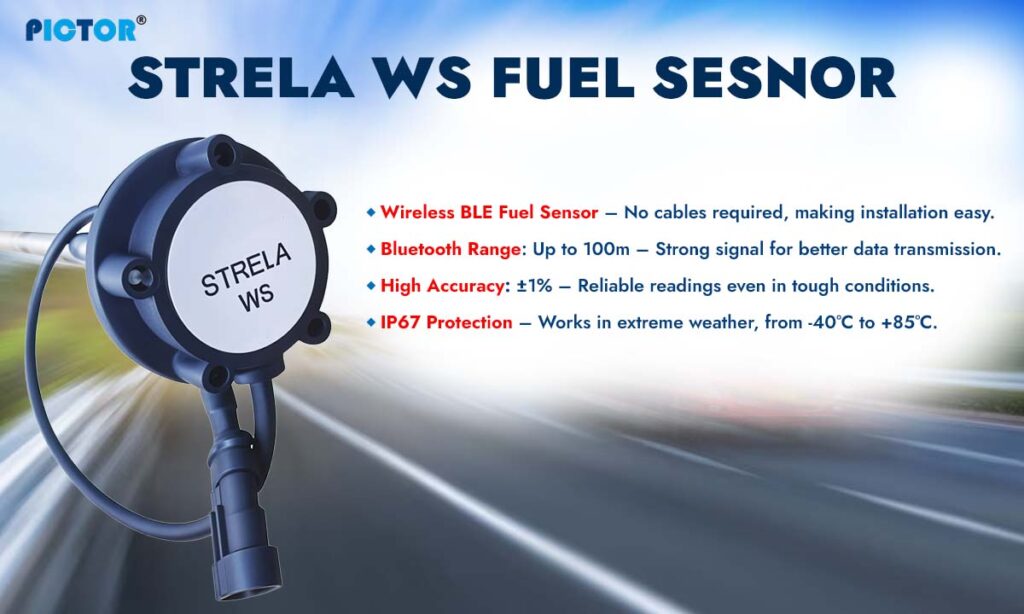
Wireless BLE Fuel Sensor – No cables required, making installation easy.
Bluetooth Range: Up to 100m – Strong signal for better data transmission.
High Accuracy: ±1% – Reliable readings even in tough conditions.
IP67 Protection – Works in extreme weather, from -40°C to +85°C.
Best for: Large truck fleets needing easy-to-install fuel tracking.
2. Wireless Fuel Level Sensor: Strela WD
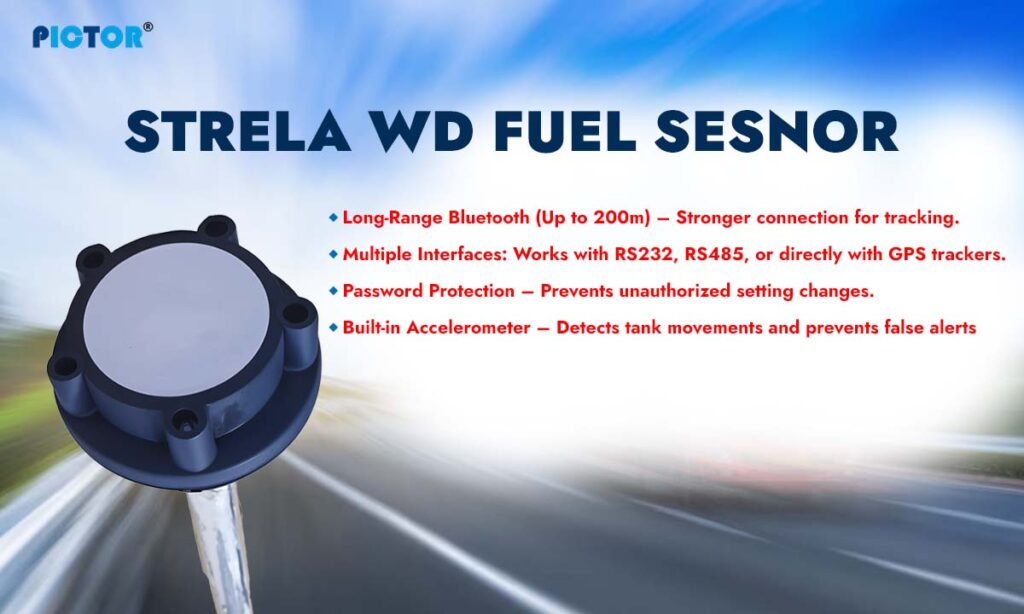
Long-Range Bluetooth (Up to 200m) – Stronger connection for real-time tracking.
Multiple Interfaces: Works with RS232, RS485, or directly with GPS trackers.
Password Protection – Prevents unauthorized setting changes.
Built-in Accelerometer – Detects tank movements and prevents false alerts.
Best for: Fleets that require wireless fuel monitoring over long distances.
3. Fuel Level Indicator: Strela D485
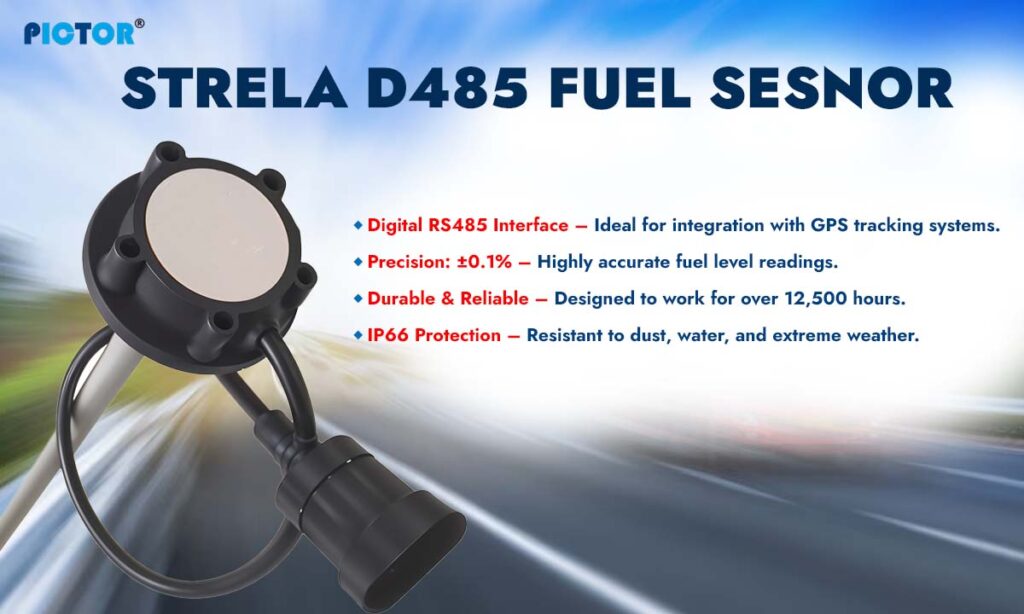
Digital RS485 Interface – Ideal for integration with GPS tracking systems.
Precision: ±0.1% – Highly accurate fuel level readings.
Durable & Reliable – Designed to work for over 12,500 hours.
IP66 Protection – Resistant to dust, water, and extreme weather.
Best for: Truck owners who need accurate fuel tracking with a long-lasting device.
3. CLS2 Fuel Level Sensor
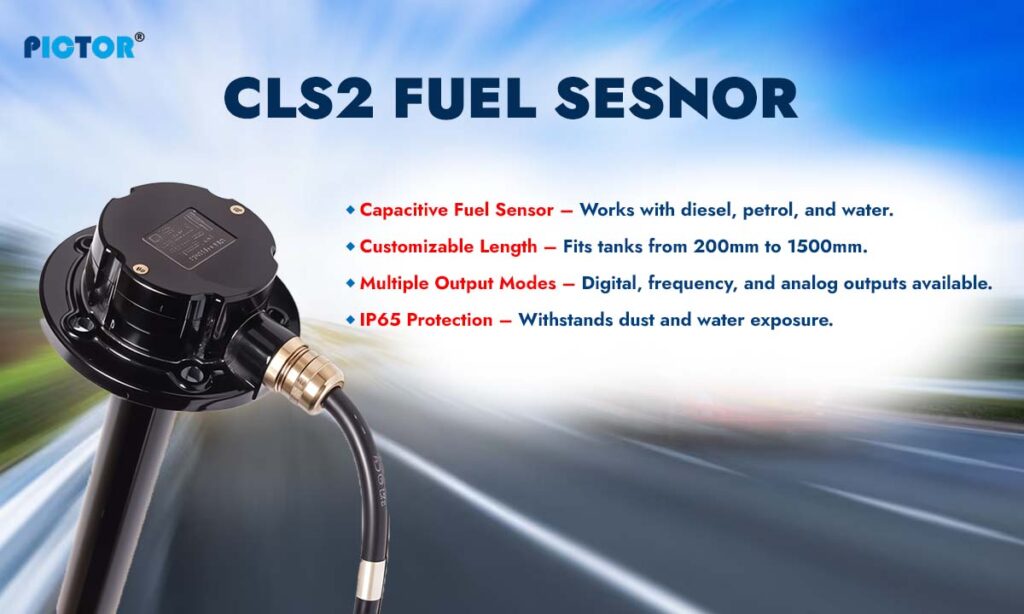
Capacitive Fuel Sensor – Works with diesel, petrol, and water.
Customizable Length – Fits tanks from 200mm to 1500mm.
Multiple Output Modes – Digital, frequency, and analog outputs available.
IP65 Protection – Withstands dust and water exposure.
Best for: Fleet operators who need flexible installation options.
Conclusion: Choosing the Perfect Fuel Sensor for Your Truck
In conclusion, selecting the perfect fuel sensor for your truck fleet is a critical decision that can significantly impact operational efficiency and cost management. With the right knowledge of the types of sensors available, the factors to consider, and the importance of accurate specifications, fleet managers can make informed choices that align with their specific needs. The benefits of high-quality sensors, including accuracy, durability, and advanced features, further emphasize the value of investing in reliable technology.
Moreover, understanding the installation process and committing to regular maintenance will ensure that your fuel sensors perform optimally over time. By keeping an eye on the market and considering top brands known for their quality, fleet managers can find the best sensor solutions tailored to their operations.
Ultimately, the right fuel sensor not only enhances fuel efficiency but also contributes to the overall performance of your fleet. By leveraging this guide, you can confidently choose the best fuel sensor, leading to improved management of your truck fleet, reduced costs, and maximized performance on the road.
Pictor Telematics: Leading the Way in GPS Tracking and Telematics Solutions
Leave a Reply